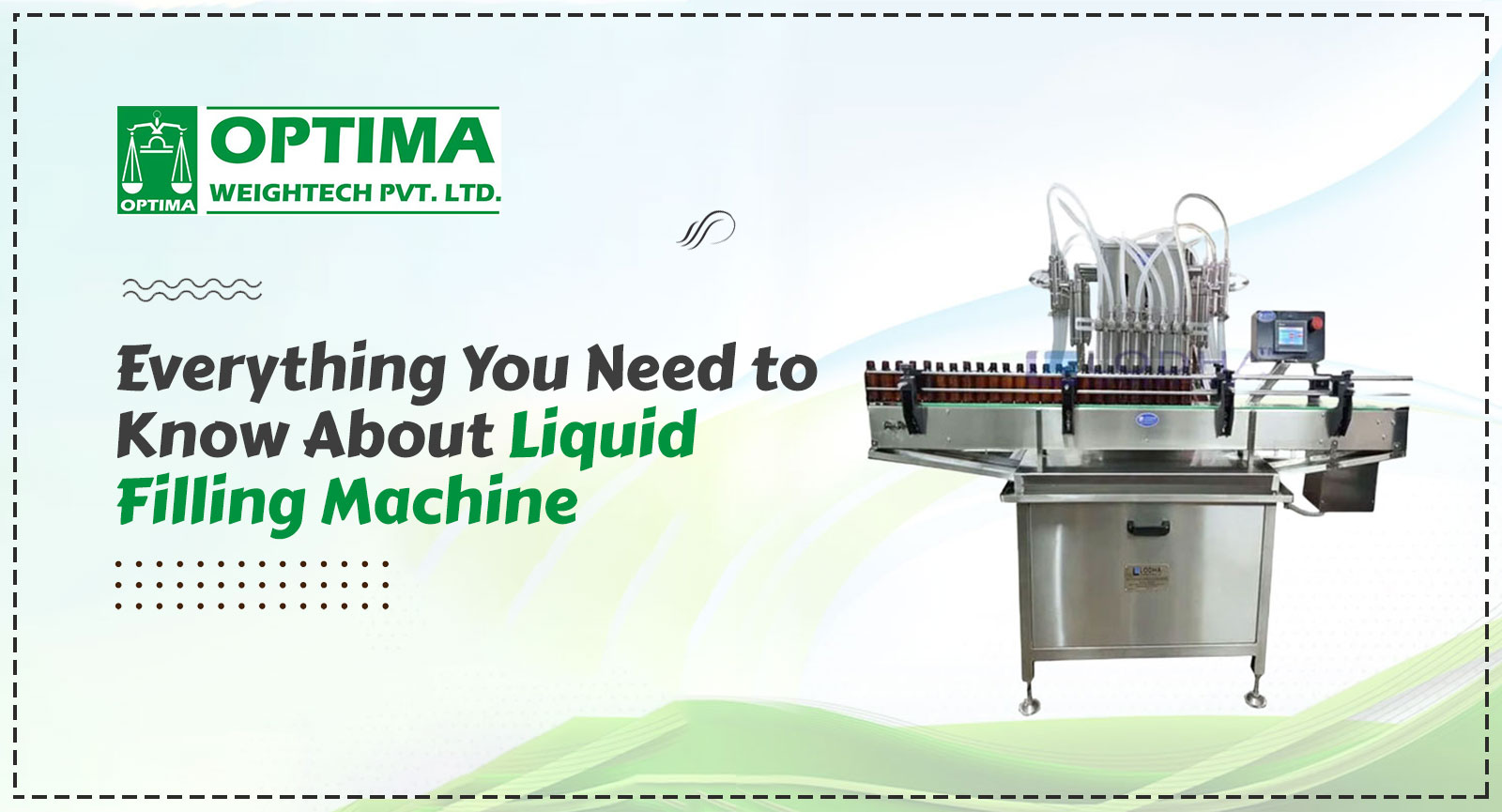
Everything You Need to Know About Liquid Filling Machine
The liquid-filling machines are the automated bottle-filling machines that are used in industrial processing to pack the bottles precisely. They play a vital role in improving productivity, reducing human error, and optimizing factors like speed, precision, and reliability. The liquid filling machine is available in automated as well as semi-automated and is used in industrial production facilities. In this post, we will dive into the details of the liquid-filling machine.
What is a Liquid Filling Machine?
Components of the Liquid-Filling MachineIt is a versatile device which consists of many individual parts:
It is the very first step of the filling process. The bottles are manually placed into the feeding mechanism. Depending on the filling head number, there are different types of bottle feeders to choose from.
It is important for the liquid filling machine. It is used for carrying containers throughout the filling line. The speed and the size of the conveyor belt can also be adjusted according based on certain demands. It will make the operations more smooth and efficient.
It is the major tool for the operations. It controls the direction as well as the flow of liquid. Based on how thick or thin the liquid is, there are different kinds like the straight-through nozzle, purge nozzle, and overflow nozzle.
The straight-through ones are the most common and can be used for filling so many kinds of liquids. It enables the liquid to flow smoothly.
The purge nozzle is used to remove air from containers before or after filling. It reduces the chances of degradation and contamination of any kind of the product.
The overflow nozzle fills the containers to a consistent level. It pushes out the liquid until it reaches a certain point.
It is an interactive process that allows the operators to monitor the filling process and input parameters like the filling volume and the speed.
It securely seals the containers after they are filled, ensuring proper closure.
Importance of Liquid Filling Machine
There are many benefits of the liquid filling machine for industrial packing purposes.
Integrated with advanced features, the liquid filling machine ensures precise and quick filling of the bottles. It reduces the cost of labor and increases the production capacity.
The machine can fill the liquid in the specified quantities. It improves the consistency and quality of the product. It prevents errors in the manual filling process and ensures that the products are accurately packed according to the given standards.
Hygiene is of utmost importance in the food and medicine production company. The products are filled in a clean and sterile manner. The risk of contamination and spoiling the product is reduced.
The equipment is flexible and this machinery can fill the liquids of different viscosities and properties. It thus allows the manufacturers to touch a wide range of markets and quickly fulfill the demands of the customers.
Wrapping Up…
The liquid filling machine is an essential piece of equipment for enhancing production efficiency and accuracy. By understanding the components and usage of the machine you will be able to select the right kind of machine to fulfill your operational needs.
It is essential to have a great-quality machine from manufacturers like Optima Weightech Pvt. Ltd. Their liquid filling machine is made with advanced technology. They provide various benefits like less waste, fast filling speeds, and simple controls, which make them effective for liquid filling operations.