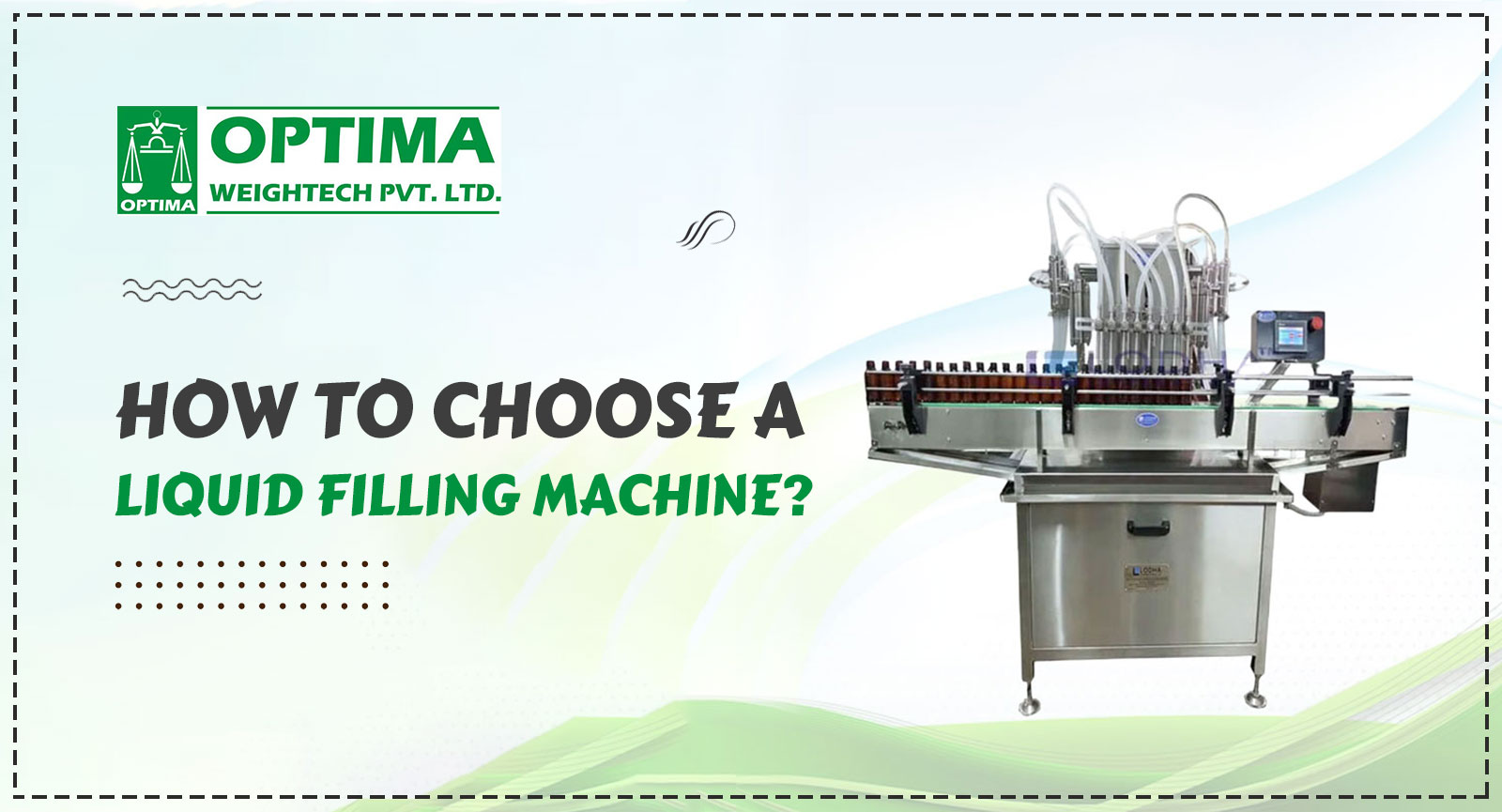
How to Choose a Liquid Filling Machine?
The liquid filling industry has done a great job of offering a plethora of highly customized filling machines while offering little to no guidance or explanation to help you navigate the landscape and make informed decisions. This deliberate tactic has served the filling equipment manufacturers well, as it often results in a phone call from a frustrated and vulnerable prospective client.
Today, we hope to lift the veil of confusion and provide you with seven critical criteria to consider when selecting your next liquid-filling machine.
Choose the Right Filling Methods
When it comes to choosing the right filing machines, there are several things to consider:
Method of Filling:
The consistency of your liquid is one of the most important elements to consider when selecting a filling technique. However, other considerations, such as manufacturing and packaging, can also influence your decision. The following are some of the ones commercially available:
Gravity Filling Machine: they’re ideal for low, consistent liquids with no granular. The liquid flows down into the jars due to gravitational force.
Piston Filling Machine:It can handle semi-solids and fluids containing particles, and it can manage thin to thick densities. Piston fillers are apt for the pharmaceutical industry or cosmetic products since they discharge substances in exact proportions with minimum waste.
Kind of Fillers:
Can Filler:A can filler equipment fills a variety of container types with a product in various forms, either volumetrically or quantitatively.
Tin Filler:Tin-filling machines are used to fill tins in the chemicals, cuisine, and other sectors. These tins are either made of steel or, rather, a small piece of metal sheet that makes up the body of the container.
Jar Filling Machine:Filling machines for jars are well-known in the market for their capability to efficiently manage the demands of the volumetric filling of fluids with low and high flow rates.
Automation Level:
In an automated packing line, such as a filling, topping, and branding line, an automated filling machine directs, organizes, fills, and then releases bottles. Choose the right modular can packaging machine and design the right connection to streamline your packaging line. You will have to weigh the practicality of automation versus cost and space constraints when deciding on the optimal amount of automation for your sealing gear:
Automatic filling machine:The automatic liquid filling machines are designed to work on their own. They have excellent performances.
Semi-automatic filling machine:Though some of its operations are automated, it requires human labor for precise operations.
Ease of Operations:
When you purchase a product, you need to ensure that they are easy to use. Otherwise, ensure that you get the right manual to help you with the operation of your machine.
Cleanliness and Maintenance Requirements:
Prioritize a machine that simplifies cleanliness and upkeep. Regular maintenance ensures longevity, meaning you should opt for machines designed with ease of cleaning in mind. Look for features like easily accessible components and readily available spare parts to streamline this process.
A well-maintained machine not only guarantees long-term reliability but also minimizes costly production halts, ensuring your operation runs smoothly without unexpected downtimes. Opting for such machinery is crucial in maintaining the efficiency and productivity of your detergent filling line, ultimately safeguarding the seamless flow required to meet customer demands effectively.
Final Words…
Choosing the right filling machine for your business involves understanding your product’s specific needs and the capabilities of different machines. Additionally, industry-specific machines ensure compliance with standards and meet the unique demands of different sectors. By selecting the appropriate liquid filling machine from the top manufacturers like Optima Weightech Pvt. Ltd., you can enhance efficiency, maintain product quality, and increase overall productivity.